wildebus
Full Member
- Messages
- 7,463
There is a lot of discussion of B2B Chargers, and their various merits or otherwise over the basic Relay type of Split Charger.
Next week I plan to do some testing on these to obtain a profile of just what kind of charge they provide and what the users can expect when they use a B2B or when they use direct alternator type charging through a relay. This might help understand what size (in Amperage) of B2B is suitable and the time they can expect a battery to recharge (and what the impact is for differing sizes).
I thought I would first post my proposed test setup so if anyone would like to suggest any improvements (within the kit I have available!)
Power Source.
Now I don't intend to drive around for hour after hour to have the alternator running, or idle the van engine all day, so I will be using a 120A Charger as the 'alternator', set at an output voltage that is typical of that presented to a B2B or Relay by the alternator AND taking any voltage losses in mind at the end of a typical 4 Metre run of 16mm cable - so probably I will set the charger to around 13.9V (but will check the cable loss charts to confirm)
This Power Source will be cabled up to the charger being tested. I will also connect a 100Ah fully charged battery in parallel between Power Source and Charger to act as a Pseudo-Starter Battery to simulate the same kind of actual setup you would have in a vehicle.
Leisure Batteres.
This test will be limited by the battery bank I have available. My plan is to start each test with my 380Ah AGM Battery Bank discharged to 50% SOC, so as low as you would want to go on Lead Acid usually and will also give the best test for the chargers as will cover the full charging range from Empty (in usuability terms) to Full.
All loads will be minimied during the test, so lights will be off, no heating, fridge will be off, etc. I will have a load in terms of monitoring hardware. These will be the same for all chargers. I'll also have the Solar MPPT Charger turned off so that doesn't skew anything.
Battery Chargers.
The point of the test will be to check different options in terms of charging methods and capacities. It is not to compare different models and makes of equivalent specifications.
These are the systems I have lined up to evaluate:
So the above will provide a good range of current capabilities as well as different approaches.
As mentioned, for each Charger the testing will start with the Battery Bank at 50% SOC as reported by the Victron VRM and will end when the VRM reports the Battery Bank at 100% SOC.
This will be the target, but it is possible some chargers will never get the battery to 100% due to voltage limits, so I will also look at a secondary target of maybe -5Ah or -10Ah from full to be able to compare (seeing this potential sitution is in fact part of the reason for testing)
I also have a Control Benchmark to compare each result as a comparative.
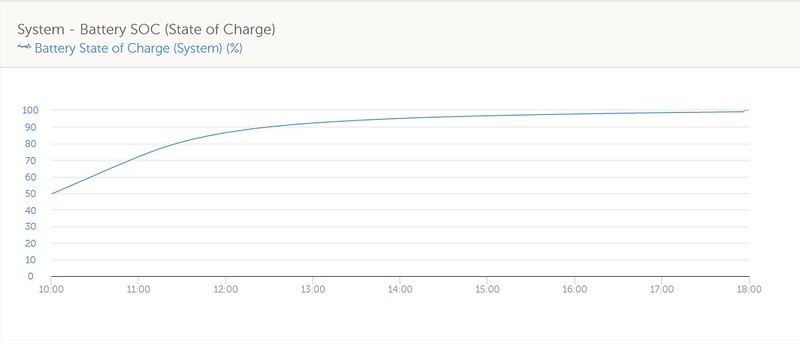
This is the chart of a 95A Mains Charger recharging the same bank from 50% to 100%.
This took 8 Hours. How long will a 20A, 30A or 40A charger take? This will be interesting to see
So that is the plan. I would be interested in comments and if there are any suggestions for the testing, or if anyone sees an issue with the test setup?
(Note that this test will be carried out in my campervan so ambient temps could vary which I cannot control of course)
Next week I plan to do some testing on these to obtain a profile of just what kind of charge they provide and what the users can expect when they use a B2B or when they use direct alternator type charging through a relay. This might help understand what size (in Amperage) of B2B is suitable and the time they can expect a battery to recharge (and what the impact is for differing sizes).
I thought I would first post my proposed test setup so if anyone would like to suggest any improvements (within the kit I have available!)
Power Source.
Now I don't intend to drive around for hour after hour to have the alternator running, or idle the van engine all day, so I will be using a 120A Charger as the 'alternator', set at an output voltage that is typical of that presented to a B2B or Relay by the alternator AND taking any voltage losses in mind at the end of a typical 4 Metre run of 16mm cable - so probably I will set the charger to around 13.9V (but will check the cable loss charts to confirm)
This Power Source will be cabled up to the charger being tested. I will also connect a 100Ah fully charged battery in parallel between Power Source and Charger to act as a Pseudo-Starter Battery to simulate the same kind of actual setup you would have in a vehicle.
Leisure Batteres.
This test will be limited by the battery bank I have available. My plan is to start each test with my 380Ah AGM Battery Bank discharged to 50% SOC, so as low as you would want to go on Lead Acid usually and will also give the best test for the chargers as will cover the full charging range from Empty (in usuability terms) to Full.
All loads will be minimied during the test, so lights will be off, no heating, fridge will be off, etc. I will have a load in terms of monitoring hardware. These will be the same for all chargers. I'll also have the Solar MPPT Charger turned off so that doesn't skew anything.
Battery Chargers.
The point of the test will be to check different options in terms of charging methods and capacities. It is not to compare different models and makes of equivalent specifications.
These are the systems I have lined up to evaluate:
- 100A HC Cargo VSR - Essentially just a battery connecting device, but I will run the "alternator" though this for completeness.
- 40A Redarc BCDC1240 Battery to Battery Charger - This is a unit I have been running in my Camper for a while.
- 30A Ablemail Battery to Battery Charger - This is a new unit to me but looks promising. I have this for evaluation following a meeting yesterday with the owner of Ablemail and though I would add this to the test portfolio.
- 20A Victron Mains Charger + 500W Inverter - This will be an extended test on the "Inverter as a Split Charger" idea I posted about before, testing the concept in an identical way to the B2Bs and VSR.
So the above will provide a good range of current capabilities as well as different approaches.
As mentioned, for each Charger the testing will start with the Battery Bank at 50% SOC as reported by the Victron VRM and will end when the VRM reports the Battery Bank at 100% SOC.
This will be the target, but it is possible some chargers will never get the battery to 100% due to voltage limits, so I will also look at a secondary target of maybe -5Ah or -10Ah from full to be able to compare (seeing this potential sitution is in fact part of the reason for testing)
I also have a Control Benchmark to compare each result as a comparative.
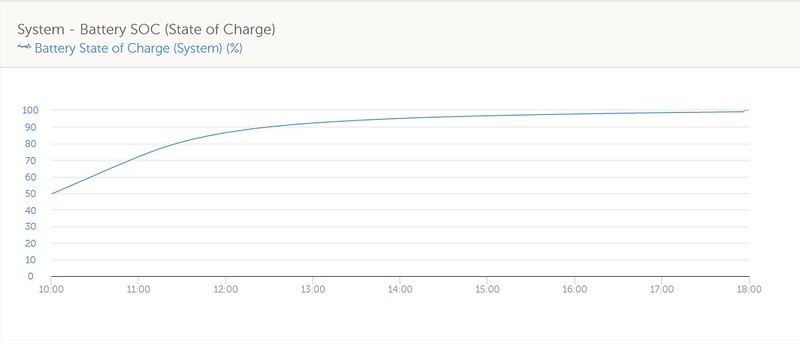
This is the chart of a 95A Mains Charger recharging the same bank from 50% to 100%.
This took 8 Hours. How long will a 20A, 30A or 40A charger take? This will be interesting to see
So that is the plan. I would be interested in comments and if there are any suggestions for the testing, or if anyone sees an issue with the test setup?
(Note that this test will be carried out in my campervan so ambient temps could vary which I cannot control of course)