Ok, so I have completed the testing
Got some interesting results and that has caused me to change my thoughts a little on which options to go for in which situations
So Recap on what I tested, how I tested and some caveats.
Used a
Victron Multiplus set at a constant 13.9V and a maximum of 95A to replicate a fairly typical Alternator output.
The test assumes the 'alternator' is always outputing up to this level. In real life, when the engine is idling, the alternator output may be reduced.
Once the test started, it carried on until done. So there are no "rest breaks" like you would usually have when driving.
And this is only relevant for Lead Acid Technology, NOT Lithium.
What did I test?
Used the
Victron Multiplus in its normal Multistage 'Smart' mode as a control. This represents the best possible charging I have available for my Camperbus
Then switching it to the 'Alternator' style output, I tested:
140A HC Cargo VSR
40A Redarc BCDC1240 B2B Charger
30A Ablemail B2B Charger
20A
Victron IP22 Mains Charger powered by 500W MSW
Inverter powered by the 'Alternator'.
All tests were to recharge a 12V 380Ah AGM
Battery Bank that had previously been discharged to 50% SOC in precisely the same way and the batteries fully recharged between tests.
So a fair variety of different output ratings and 3 different approaches to charging.
How do they compare?
Well this is a graph of the 5 different charging tests carried out showing how the SOC (State of Charge) increased over time for each of them and how long it took
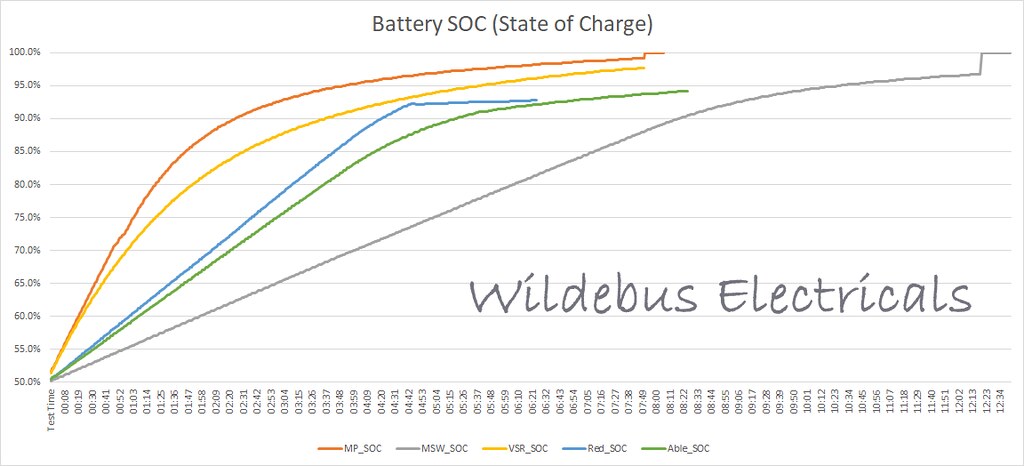
BT - Summary SOC by
David, on Flickr
As you would except, the
Multiplus in native mode (the RED line) is the best performing device. But even this unit still takes nearly 8 hours to fully recharge a 380AH
Battery Bank from 50% SOC.
The next best method is actually the VSR. This tracks the
Multiplus quite well, but is not as effective because there are losses in the Relay and cabling, plus the maximum voltage is 0.5V lower.
This lower voltage will prevent the
battery ever getting a full charge BUT the increased current would make up for that (there is a gotcha about this later on). So for MY setup, the most effective option would appear to be the basic VSR option rather than B2Bs costing hundreds of pounds!
The two B2Bs start to close the gap but not until 4:30 Hours later.
What I saw and I am not sure if it is commonly known is both B2Bs (which are different makes)appeared to switch to Float mode after a set length of time - 4:30 in the case of the Redarc and 5:30 for the Ablemail. This is before Charging was complete.
In the case of the Redarc, the float voltage went down to around 13.2V - this level is actually not enough to provide any charge (which is why the blue line just flattens until I stopped the test). The Ablemail float voltage was 13.8V, which is similar to the alternator output. The effect is that charging continues at a reduced rate and the SOC increase slows of course.
Finally the 20A Charger +
Inverter is a good steady line and eventually provides a full charge, but being only 20A takes quite a while
This is what the voltage outputs look like for the different chargers
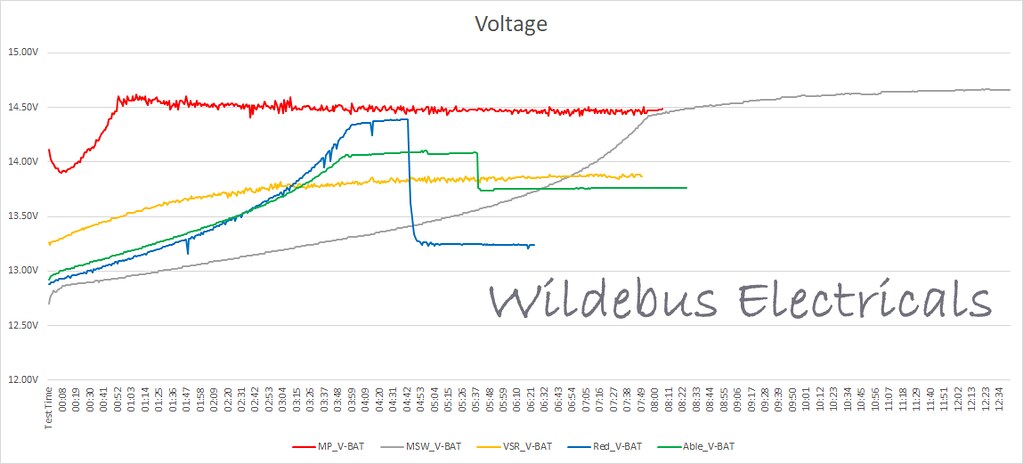
BT - Summary Voltage by
David, on Flickr
Shows quite a variety of approaches here
The initial voltage levels are down to the current going in so the voltages are gradually going up while the (smart) chargers are in bulk mode.
The
Victron Chargers (this includes the
Inverter test) go up to over 14.5V as they have temperature compensation available.
The Redarc goes up to 14.4V (the basic target for Lead Acid) before dropping to a surprisingly low 13.2V float
The Ablemail goes up to 14.1V before dropping to 13.8V for float
Five different charging options; Five very different results.
So any conclusions?
The choice of what capacity charger to go for depends of how large a
battery bank you have and how quick a recharge you need
As can be seen from the Graphs, the 20A charger will take twice as long as the 40A charger to get to Absorption mode but will not take twice as long to fully recharge. As an extreme example, the 20A charger is nominally just around 20% of the capacity of the 95A Mains Charger, but actually completes its charge from 50% to full in just over 70% extra time in my testing (12:30 hours instead of 7:50 hours)
As a point to note, the data I am seeing and from the conversations I have had with B2B manufacturers, you can reckon that for the typical 30A B2B Charger, it will take around 1Hr per 100Ah to go from 50% SOC to completing the bulk charge.
Once the charger goes into Absorption mode, the current starts to drop fairly fast and the actual current capability of the charger becomes much less of a factor.
When selecting the charger, also bear in mind the basic rule of Lead Acid Batteries - you should typically charge at no faster a rate then 0.2C e.g. A maximum of 20A per 100A of
battery. Some people and some
battery makers recommend 0.1C (10A per 100Ah). My own batteries happen to be ok for 0.25C which is why I set my
Multiplus for 95A (0.25C of 380Ah).
So if you have 200Ah of Lead Acid Batteries, you probably want a charger no greater than 40A maximum output for example. You won't see 95A going into the
battery for more then a couple of minutes at the most (unlike in my example) with just 200Ah and you would run the risk of excessic charge rate as well. In this case, the case for a B2B over a VSR is much more convincing.
For this reason on Maximum Charge Rates, the opportunity for getting the full usage of a B2B like a CTEK with SmartPass (to give a 100A capability) for the typical Motorhome
Battery Bank is very limited I would say.
This chart shows the Current delivery of the different chargers to help illustrate what I am meaning
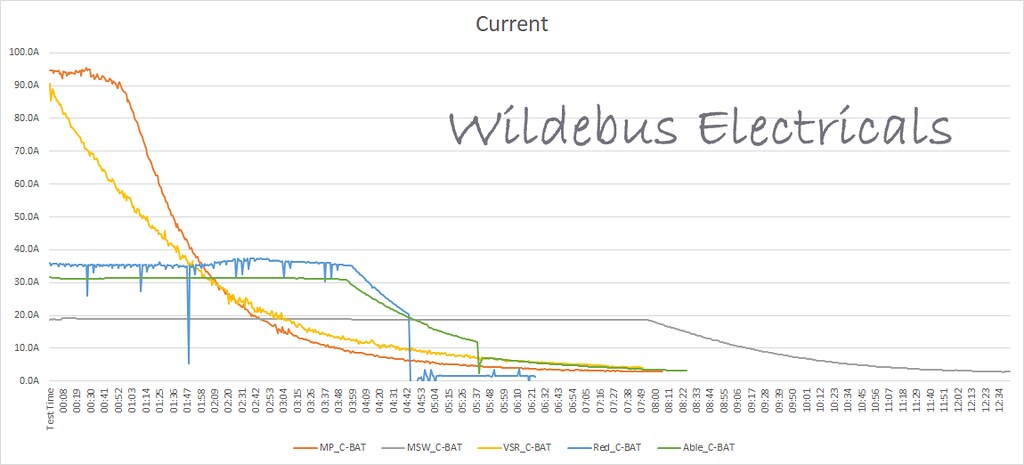
BT - Summary Current by
David, on Flickr
Lots of info. Well done to anyone who has made it this far! Any questions please shout.